Manutenção de Automação Industrial: As Melhores Práticas para Garantir Eficiência
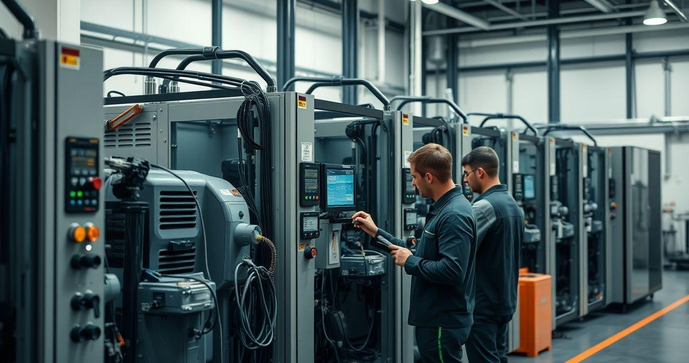
Por: Ingrid - 18 de Março de 2025
Importância da Manutenção na Automação Industrial
A manutenção na automação industrial é crucial para assegurar o funcionamento contínuo e eficiente dos sistemas. Estes sistemas, que frequentemente incluem diversas máquinas e equipamentos interconectados, precisam de suporte regular para evitar falhas que podem causar interrupções significativas na produção.
Um dos principais benefícios de realizar uma manutenção proativa é a prevenção de paradas não programadas. Quando os equipamentos são mantidos de forma regular, é possível identificar e corrigir problemas antes que eles se tornem críticos. Isso não só protege a linha de produção, mas também minimiza custos associados a reparos emergenciais e perda de receita.
Além disso, a manutenção adequada aumenta a vida útil dos equipamentos. Sistemas e máquinas que passam por manutenção regular tendem a ter um desempenho mais confiável e duradouro. Essa durabilidade é essencial em um ambiente industrial, onde o desgaste constante é uma realidade, e a continuidade operacional é vital.
Outra razão que justifica a importância da manutenção é a segurança. A inspeção regular pode revelar problemas que representam riscos não só para os equipamentos, mas também para os trabalhadores. A manutenção preventiva garante que todos os sistemas operem dentro das normas de segurança, evitando acidentes e protegendo a saúde dos colaboradores.
A eficiência energética também é um fator relevante. Equipamentos mal mantidos podem consumir mais energia do que o necessário. Ao otimizar o desempenho de máquinas através da manutenção, as empresas podem reduzir seus custos operacionais e contribuir para práticas mais sustentáveis.
Por fim, a manutenção na automação industrial é um investimento estratégico. As empresas que priorizam esta prática não apenas garantem a eficiência e a segurança de suas operações, mas também se posicionam melhor no mercado, tornando-se mais competitivas.
Principais Tipos de Manutenção Utilizados
Na automação industrial, diversos tipos de manutenção são empregados para garantir o funcionamento eficiente e seguro dos equipamentos. A escolha do tipo de manutenção a ser realizada depende das necessidades específicas de cada operação e do grau de automação dos sistemas. A seguir, apresentamos os principais tipos de manutenção utilizados.
1. Manutenção Corretiva: Este tipo de manutenção é executado após a ocorrência de uma falha. A manutenção corretiva tem como foco resolver problemas que já afetaram o funcionamento dos sistemas, buscando restaurar a operação normal. Embora seja necessária, a manutenção corretiva pode resultar em paradas inesperadas e perda de produtividade.
2. Manutenção Preventiva: Este método envolve a realização de serviços programados que visam prevenir falhas antes que aconteçam. A manutenção preventiva é baseada em intervalos de tempo ou uso predeterminado, o que permite identificar e substituir componentes desgastados, garantir que os sistemas operem de forma eficiente e prolongar a vida útil dos equipamentos.
3. Manutenção Preditiva: A manutenção preditiva utiliza tecnologias de monitoramento e análise de dados para prever falhas antes que elas se concretizem. Com o uso de sensores e sistemas de monitoramento, as organizações podem coletar informações em tempo real sobre o desempenho de seus equipamentos, permitindo intervenções planejadas que minimizam o tempo de inatividade.
4. Manutenção Detectiva: Essa abordagem tem como objetivo detectar problemas em equipamentos antes que eles se tornem críticos. A manutenção detectiva envolve inspeções regulares e a utilização de tecnologias de diagnóstico para identificar falhas iminentes. Isso facilita a solução de problemas antes que causem interrupções significativas.
5. Manutenção Proativa: A manutenção proativa visa mudar a cultura da manutenção de reativa para uma abordagem mais analítica, concentrando-se em causas raízes de falhas. Em vez de realizar reparos após a ocorrência de um problema, a manutenção proativa busca entender e eliminar as causas que levam ao desgaste e à falha dos equipamentos.
Esses tipos de manutenção são fundamentais para maximizar a eficiência operacional nas indústrias automatizadas. A combinação de diferentes abordagens pode trazer benefícios significativos, incluindo redução de custos, aumento da produtividade e melhor segurança no ambiente de trabalho.
Ferramentas e Técnicas para a Manutenção Eficiente
Para garantir uma manutenção eficiente na automação industrial, é fundamental contar com as ferramentas e técnicas adequadas. A escolha correta destas ferramentas pode otimizar o processo de manutenção, reduzindo custos e aumentando a eficácia das ações realizadas. Vamos explorar algumas das principais ferramentas e técnicas utilizadas nesse contexto.
1. Software de Gestão de Manutenção: Os softwares de Gestão de Manutenção Assistida por Computador (GMAC) permitem que as empresas planejem, rastreiem e gerenciem todas as atividades de manutenção. Essas plataformas ajudam a organizar as ordens de serviço, programar manutenções preventivas e manter um histórico detalhado dos trabalhos realizados, o que é essencial para uma gestão eficaz do ativo.
2. Tecnologias de Monitoramento Remoto: Sensores e dispositivos de monitoramento remoto são cruciais para a manutenção preditiva. Eles coletam dados em tempo real sobre o desempenho dos equipamentos, permitindo que as equipes de manutenção identifiquem anomalias e adotem medidas corretivas antes que uma falha ocorra. Isso gera um ganho significativo de eficiência, já que as intervenções podem ser feitas de forma planejada.
3. Análise de Vibração: A análise de vibração é uma técnica comum na manutenção preventiva e preditiva. Ela permite identificar problemas mecânicos, como desalinhamentos e desgastes em rolamentos, antes que se tornem críticos. Com o uso de equipamentos de medição, as empresas podem monitorar as vibrações das máquinas e tomar decisões informadas sobre a manutenção.
4. Termografia Infravermelha: Esta técnica é aplicada para detectar pontos de calor em equipamentos elétricos e mecânicos. A termografia infravermelha ajuda a identificar problemas como sobrecargas, conexões soltas e falhas iminentes em circuitos elétricos. Através de câmeras térmicas, os profissionais podem realizar inspeções não-invasivas, evitando descargas elétricas e interrupções nos processos.
5. Lubrificação Adequada: O uso correto de lubrificantes é fundamental para a manutenção eficiente de equipamentos. A lubrificação regular reduz o atrito e o desgaste das partes móveis, garantindo um desempenho ideal. Além disso, é importante seguir as especificações dos fabricantes em relação ao tipo e à frequência da lubrificação, o que contribui para a durabilidade dos componentes.
6. Treinamento de Equipe: Investir no treinamento contínuo da equipe de manutenção é uma técnica essencial para aumentar a eficiência das operações. Profissionais bem treinados têm mais chances de identificar problemas precocemente e realizar as manutenções de maneira eficaz. Além disso, um bom treinamento em novas tecnologias e técnicas assegura que a equipe esteja atualizada com as melhores práticas do mercado.
Ao adotar essas ferramentas e técnicas, as empresas podem não apenas melhorar a eficiência da manutenção, mas também criar um ambiente operacional mais seguro e produtivo. Integrar tecnologia e capacitação na equipe é crucial para o sucesso das operações industriais automatizadas.
Desafios Comuns na Manutenção de Sistemas Automatizados
A manutenção de sistemas automatizados apresenta vários desafios que podem impactar a eficiência operacional e a segurança das operações. Compreender esses desafios é essencial para que as empresas desenvolvam estratégias eficazes e garantam a continuidade da produção. Aqui estão alguns dos principais desafios enfrentados na manutenção de sistemas automatizados.
1. Complexidade dos Sistemas: Os sistemas automatizados atuais são frequentemente compostos por diversos componentes interconectados, desde sensores até controladores e atuadores. Essa complexidade pode dificultar a identificação de problemas, tornando as intervenções mais demoradas e complicadas. As equipes de manutenção precisam ter um entendimento profundo dos sistemas para diagnosticar e resolver falhas de forma eficaz.
2. Falta de Documentação: A ausência de documentação adequada sobre o sistema, incluindo esquemas elétricos, manuais de operação e históricos de manutenção, pode levar a diagnósticos errôneos e soluções inadequadas. Sem informações sólidas, as equipes podem gastar tempo vital tentando descobrir como os sistemas realmente funcionam e quais intervenções são necessárias.
3. Tempo de Inatividade Indesejado: A necessidade de parar uma linha de produção para realizar manutenções pode resultar em custos significativos e perda de receita. Planejar manutenções preventivas e preditivas é crucial, mas mesmo assim, imprevistos podem ocorrer, resultando em paradas não programadas. O desafio é equilibrar a manutenção necessária com a demanda por produção constante.
4. Integração de Novas Tecnologias: À medida que a tecnologia avança, a integração de novos sistemas e equipamentos na infraestrutura existente pode gerar dificuldades. A falta de compatibilidade entre equipamentos mais antigos e novas tecnologias pode resultar em falhas de comunicação e desempenho inadequado, exigindo adaptações e, em alguns casos, substituição de componentes.
5. Treinamento de Pessoal: A capacidade da equipe de manutenção em lidar com tecnologias emergentes e sistemas complexos pode ser um desafio significativo. Investir em treinamento contínuo é fundamental, mas pode ser dispendioso e exigir tempo. Sem o seu devido preparo, os profissionais podem ter dificuldades em solucionar problemas rapidamente e em realizar manutenções adequadas.
6. Custo de Manutenção: A manutenção pode se tornar um custo significativo para a empresa, especialmente se não for planejada adequadamente. O custo de peças de reposição, ferramentas especializadas, e treinamento pode impactar o orçamento. Por isso, é vital que as organizações implementem uma estratégia de manutenção econômica que maximize o retorno sobre o investimento.
Enfrentar esses desafios requer uma abordagem estratégica que inclua planejamento adequado, utilização de tecnologias de monitoramento, atualização constante do conhecimento da equipe e documentação completa dos sistemas. Ao lidar proativamente com esses obstáculos, as empresas podem garantir uma operação automatizada mais eficiente e resiliente.
Treinamento da Equipe para Procedimentos de Manutenção
O treinamento da equipe para procedimentos de manutenção é um componente essencial para assegurar a eficiência e a segurança nos ambientes de automação industrial. Profissionais bem preparados são capazes de lidar com tecnologias complexas e solucionar problemas de maneira eficiente, minimizando paradas de produção e melhorando a qualidade do trabalho. Aqui estão alguns aspectos importantes para desenvolver um programa de treinamento eficaz.
1. Avaliação de Necessidades: Antes de começar os treinamentos, é crucial realizar uma avaliação das necessidades da equipe. Isso envolve identificar lacunas de conhecimento, habilidades e experiências em relação aos sistemas automatizados que a equipe opera. A partir dessa avaliação, é possível criar um programa de treinamento adaptado às especificidades e desafios do ambiente de trabalho.
2. Conteúdo Atualizado: A tecnologia na automação industrial está em constante evolução, portanto, o conteúdo dos treinamentos deve ser atualizado regularmente. É fundamental incluir informações sobre novos sistemas, equipamentos e tendências emergentes para que a equipe esteja sempre informada e preparada para lidar com os avanços no campo.
3. Métodos de Ensino Diversificados: Adotar uma variedade de métodos de ensino pode aumentar a eficácia do treinamento. Combinações de aulas teóricas, demonstrações práticas, simulações e treinamento em campo ajudam os colaboradores a desenvolver competências práticas. O uso de tecnologias como realidade aumentada e aprendizado virtual também pode enriquecer a experiência de aprendizado.
4. Foco em Segurança: O treinamento deve enfatizar a importância da segurança em todas as operações de manutenção. Os profissionais precisam conhecer os riscos associados aos sistemas automatizados e entender procedimentos de segurança, como o uso de Equipamentos de Proteção Individual (EPI) e protocolos de desligamento seguro dos equipamentos. Isso não só protege os funcionários, mas também contribui para a integridade dos sistemas.
5. Treinamento Contínuo: A manutenção não deve ser uma atividade de uma só vez, assim como o treinamento. Implantar programas de reciclagem periódica é vital para garantir que a equipe mantenha suas habilidades atualizadas e siga as melhores práticas. A manutenção contínua de conhecimentos também diminui o risco de obsolescência das habilidades dos funcionários.
6. Avaliação e Feedback: Após a realização do treinamento, é importante avaliar a eficácia do programa através de testes práticos e feedback dos participantes. As avaliações permitem verificar a retenção do conhecimento e a eficácia do treinamento. O feedback pode ajudar a ajustar e melhorar futuras sessões, garantindo que a equipe receba uma formação cada vez mais relevante e eficaz.
Em resumo, um programa de treinamento bem elaborado e focado não apenas melhora a competência da equipe em procedimentos de manutenção, mas também aumenta a eficiência operacional e a segurança no ambiente de trabalho. Investir no desenvolvimento contínuo dos profissionais é uma estratégia importante para o sucesso a longo prazo nas operações de automação industrial.
Tendências Futuras na Manutenção de Automação Industrial
A manutenção de automação industrial está em constante evolução, impulsionada por inovações tecnológicas e a crescente demanda por eficiência. Para se manter competitivas, as empresas devem estar atentas às tendências futuras que moldarão o setor. Aqui estão algumas das principais tendências que podem impactar a manutenção nos próximos anos.
1. Internet das Coisas (IoT): A integração da Internet das Coisas (IoT) nos sistemas industriais permitirá que equipamentos e máquinas se comuniquem entre si e com plataformas de gerenciamento. Sensores conectados monitorarão dados em tempo real, proporcionando insights valiosos sobre o desempenho do equipamento. Isso facilitará a implementação de manutenções preditivas, onde as intervenções serão realizadas antes que ocorram falhas.
2. Big Data e Análise de Dados: Com a grande quantidade de dados gerados pelos dispositivos conectados, as empresas poderão usar análises de Big Data para melhorar suas estratégias de manutenção. Por meio da análise de padrões e tendências, as organizações poderão prever falhas, otimizar cronogramas de manutenção e tomar decisões mais informadas. Isso leva a uma maior eficiência operativa e redução de custos.
3. Realidade Aumentada (RA): A realidade aumentada está se tornando uma ferramenta valiosa para a manutenção industrial. Técnicos poderão usar óculos de RA para visualizar informações em tempo real sobre os equipamentos, receber orientações passo a passo e até mesmo colaborar com especialistas remotamente durante o reparo. Essa tecnologia pode agilizar a solução de problemas e melhorar a eficiência do treinamento.
4. Manutenção Autônoma: Com o avanço da inteligência artificial e aprendizado de máquina, a manutenção autônoma pode se tornar uma realidade. Sistemas inteligentes serão capazes de monitorar e avaliar o desempenho dos equipamentos, realizando manutenções automaticamente sem intervenção humana. Essa abordagem elimina o tempo de inatividade e reduz erros operacionais.
5. Sustentabilidade: A crescente preocupação com a sustentabilidade está influenciando as práticas de manutenção. As empresas estão adotando abordagens que priorizam a eficiência energética e a redução de desperdícios. A manutenção visando aumentar a eficiência dos equipamentos contribuindo para a redução da pegada de carbono e otimização dos recursos se tornará fundamental para as estratégias empresariais.
6. Capacitação Contínua: À medida que a tecnologia avança, a necessidade de treinamento contínuo e atualização das equipes permanecerá em alta. As empresas precisarão investir em capacitação para que seus colaboradores desenvolvam habilidades que permitam operar e manter sistemas cada vez mais complexos. O desenvolvimento de programas de formação adaptáveis e focados será essencial.
Essas tendências destacam a direção em que a manutenção de automação industrial está se movendo. Adotar essas inovações será vital para que as empresas permaneçam competitivas e eficientes. O futuro da manutenção está ligado à tecnologia, à sustentabilidade e ao constante aprimoramento das habilidades da equipe, garantindo assim uma operação industrial mais integrada e eficaz.
A manutenção de automação industrial é um elemento crucial para assegurar a eficiência e a continuidade operacional nos ambientes industriais modernos.
Ao considerar a importância dessa prática, as empresas podem implementar estratégias de manutenção proativa que não só previnem falhas, mas também aumentam a vida útil dos equipamentos e garantem um ambiente de trabalho seguro.
Através da adoção de diversas técnicas e ferramentas, bem como a capacitação contínua da equipe, as organizações podem enfrentar os desafios comuns da manutenção de forma eficaz.
As tendências futuras, como a IoT, análise de dados, realidade aumentada e práticas sustentáveis, prometem reformular ainda mais o conceito de manutenção, tornando-a mais eficiente e integrada.
Investir na manutenção não é apenas uma questão de manutenção de equipamentos, mas sim um passo estratégico que pode levar a um aumento significativo na competitividade e produtividade no mercado industrial.